Pen printing methods
Ingli Sweden has supplied the market with printed and engraved pens for more than 40 years. Each month we deliver more than a million pens, most of these produced at our in-house printing facility.
The facility consists of a large number of machines, both manual and automated, which enable us to print or engrave all types of promotional pens. Thanks to our specially trained printers and machinery specially adapted for printing pens, production can take place using secure, controlled processes while providing for a degree of flexibility that you don’t get from other printers.
We offer the following methods for printing or engraving pens:
Pad printing
Pad printing is one of the most common methods of printing pens. To get an insight into how this technology works, think back to the potato printing you did at school, but in reverse. Instead of carving a potato, we etch the design into a metal tray called a cliché. This etching is then filled with your chosen ink. Any excess is scraped off and a silicon pad presses against the design and transfers it onto the pen. A separate cliché is needed for each design and ink. Printing can be done in up to four colours from the PMS scale.
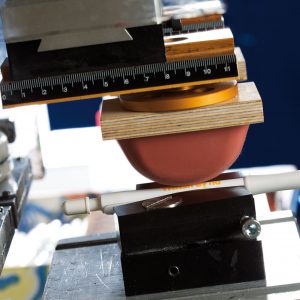
Pad printing is best suited to printing narrow or curved pens, clips, and metal pens. The advantage of using pad printing is that you can make detailed logos and small text with no loss of quality. This method also allows for printing on concave, convex, and uneven surfaces.
Screen printing
Along with pad printing, screen printing is one of the most common methods for printing on pens. In brief, this method involves using a squeegee to press the colour through a fine, stretched mesh to transfer the colour onto the pen. By producing a film with the print design and then projecting the film onto the cloth in between, you ensure that only the colour of the design passes through. Like pad printing, screen printing can be done in up to four colours, with each ink requiring a separate cloth.
Besides the short drying time and durability of the print, screen printing offers the advantage that almost the whole pen can be printed, or at least as much as the shape of the pen allows. Screen printing is also well suited to printing large volumes.
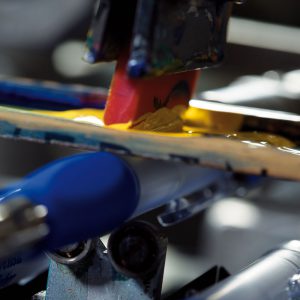
Common to both pad and screen printing is that a white subsurface or multiple layers of colour may be needed. This is similar to needing to give the furniture or walls at home two to three coats of paint to get good coverage. This is especially the case for light inks on dark surfaces, such as yellow ink on a dark blue pen. Without a white subsurface, the colour could appear green. Obviously, this is nothing you need to worry about, but it’s good to know as it could affect the print cost.
Foil printing
Foil printing is an exciting technology that offers an eye-catching, shiny end result. Printing with foil involves using a heated cylinder to apply a thin layer of foil on the intended print surface. This printing method is limited to gold or silver foil and is not suitable for printing in multiple colours or a specific ink. Pens with chrome detailing are best suited to the silver foil, while we usually recommend gold foil for pens with gold detailing.
There are two things to bear in mind with foil printing. Firstly, the pen body must be completely even in order for the cylindrical roller to have contact with the surface. Secondly, the pen cannot be frosted, as this finish will melt due to the hot temperature required for foil printing.
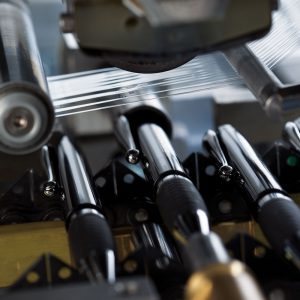
The advantages of foil printing are that the film always gives even, opaque coverage and that the shiny, glossy surface is eye-catching and exudes luxury. Despite the luxury feel, foil printing doesn’t cost much more than a regular screen or pad printing.
Digital printing
Digital printing requires a digital flatbed printer. To enable this, we have a special plate that we place the pens on. A printhead goes back and forth over the pens to transfer ink onto the pen surface. This works largely in the same way as a standard colour printer for paper in that the printing information is transferred digitally from the computer.
With digital printing, you can print in as many shades of colour as you want, as CMYK colours are used. This, of course, opens up a multitude of possibilities, both in terms of printing logos in different shades or printing images and photos.
Digital printing is best suited to thicker pens and pens with broader clips. It is also by far the best method for printing cases and gift boxes, as it allows borderless printing and printing over large areas. Another advantage of digital printing is that, regardless of the number of ink colours, the machine only has to be set up once. This results in a lower start-up cost compared with four-colour printing in the case of screen or pad printing
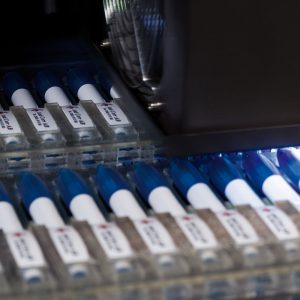
However, digital printing also has its limitations. Since a flatbed printer requires flat surfaces, and pens are cylindrical with protruding clips, the print size is limited and some locations are just impossible.
Engraving
Engraving involves amplifying light and applying electricity to create an optical beam, or more specifically a laser, which then etches a predetermined design on the product’s surface. We offer two different engraving techniques – a YAG laser and a CO2 laser. The method we use depends entirely on the type of material on the surface to be engraved. A YAG laser produces a tonal effect that matches the original material, which is often preferred to a CO2 laser, which can be used to engrave metal pens with painted surfaces.
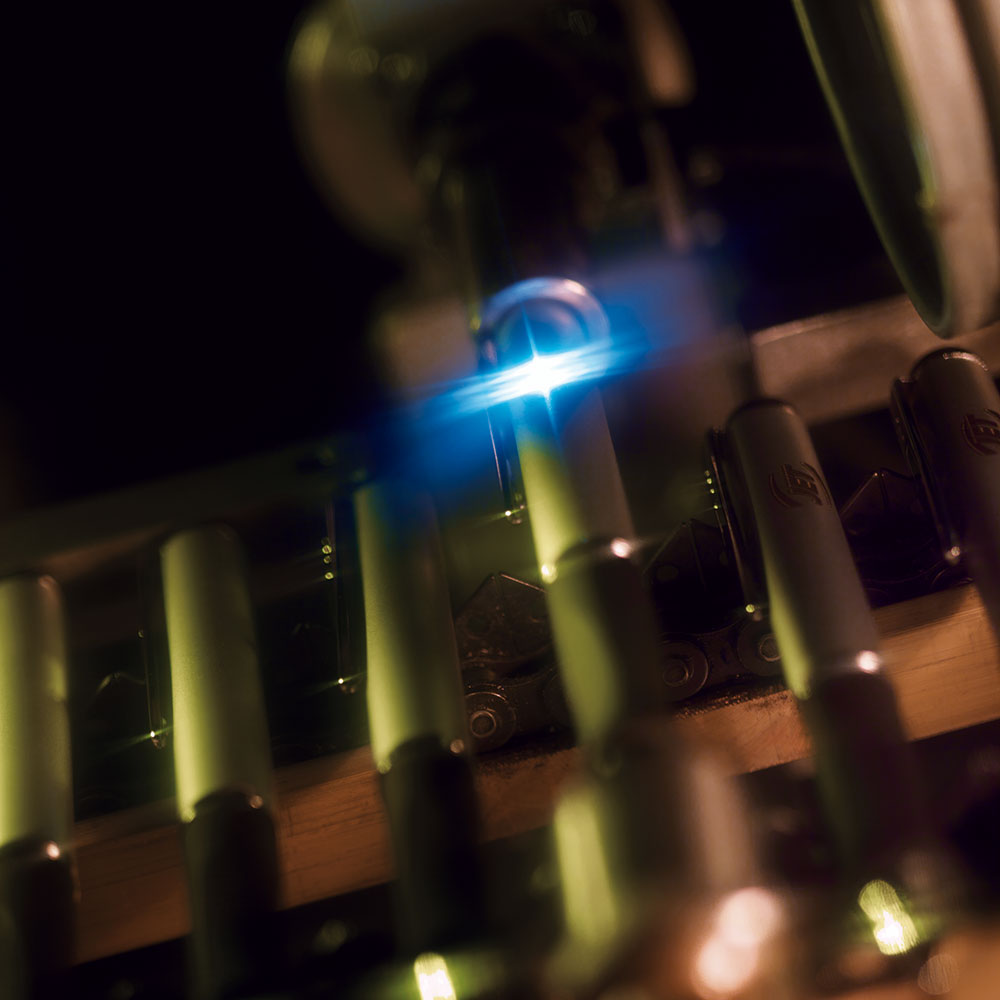
Engraving is suitable for pens that must stand up to continuous use and exposure to harsh environments. The major advantage is that engraving is permanent, as well as being eco-friendly and contact-free, with rapid, precise production. Furthermore, engraving arguably offers the most elegant finish and is well suited to more exclusive metal pens.